
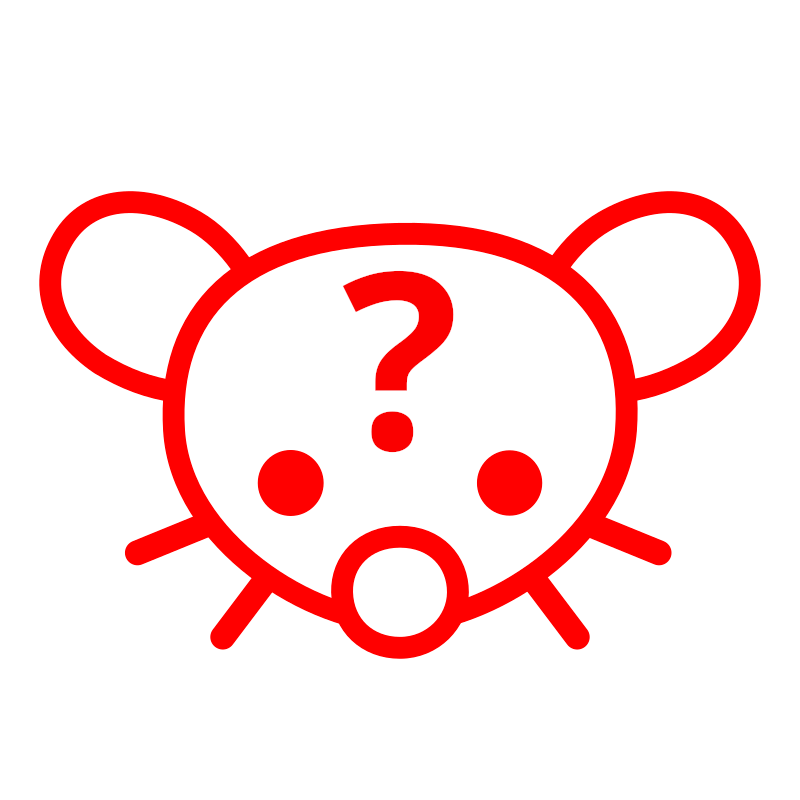
A lot of units now a days have a plastic coating on the discharge gas pipe which mostly prevents the corrosion issue. I am a refrigeration mechanic and while the condensate pan is one of the first areas I check for leaks, it also isn’t the most common area. It probably ranks in third place for frequencybof leaks on reach in units. I probably get 10x more leaks right in the evap coils. People just tend to notice the condensate pan leaks more because they’re on the high pressure side of the system so they’re going to be quick and relatively dramatic. Evap leaks can fly under the radar for years because they’re usually small and only result in gradually worsening performance.
There are also alternative condensate pan designs which use sheets of a wicking felt like material standing up in the condensate pan to increase the surface area for evaporation. That plus the warm air from the condenser fan can often work just as well as the discharge gas heated pans without the corosion issues. The reason that more companies don’t do that is because using the discharge gas for evaporating condensation also means that you’re using the condensation to precool the discharge gas so it slightly boosts the efficiency of the unit.
They use adiabatic coolers to minimize electrical cost for cooling and maximize cooling capacity. The water isn’t directly used as the cooling fluid. It’s just used to provide evaporative cooling to boost the efficiency of a conventional refrigeration system. I also suspect that many of them are starting to switch to CO2 based refrigeration systems which heavily benefit from adiabatic gas coolers due to the low critical temp of CO2. Without an adiabatic cooler the efficiency of a CO2 based system starts dropping heavily when the ambient temp gets much above 80F.
They could acheive the same results without using water, however their refrigeration systems would need larger gas coolers which would increase their electricity usage.